The oil and gas industry has been a main stay of the global economy for decades. However, market volatility, environmental concerns and poor operating performance have also challenged this industry group to adapt and innovate. Using a digital twin is one such innovation.
In the age of digital transformation, digital twin is becoming a powerful solution to energy production challenges. As an advancement from the Industrial Internet of Things (IIoT), digital twin technology is changing the oil and gas industry landscape by helping suppliers optimize asset management, increase efficiency and reduce operating costs and unplanned down time.
Digital Twin–Concept Definition
A digital twin is a dynamic, virtual representation of a physical object or system, simulating its behavior in real time. By integrating real-time operational data, historical information and advanced algorithms into a comprehensive digital model, the digital twin can predict future behavior, fine-tune operational performance and allows never-before-seen information about the behavior of the actual instance in the real world.
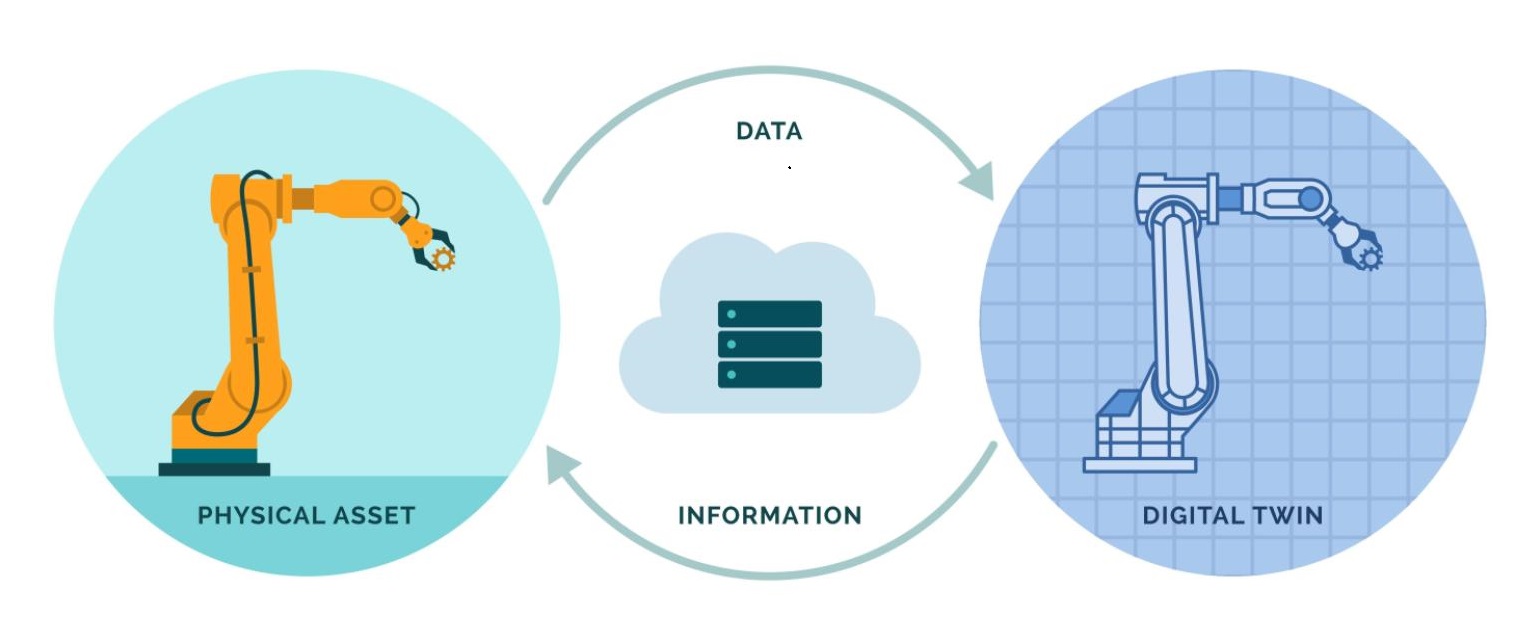
How Does a Digital Twin Upgrade Operations in the Oil and Gas Industry?
This technology was initially used by NASA to prepare for space missions, but its use cases are diverse, especially for oil and gas operators. Digital twins support the following aspects:
- Predictive maintenance: One of the most useful applications of digital twins in the oil and gas industry is predictive maintenance (PdM). In this context, a maintenance team creates a digital twin of a piece of equipment or machinery. It will continuously collect data from physical assets and use predictive analytics and machine learning algorithms to predict future performance. By continuously monitoring device performance and comparing it to the virtual version, operators can predict potential problems or failures.
- Efficient and safe operation: Digital twin technology can significantly improve operational efficiency. A digital twin can simulate different operating scenarios, helping the team understand how different operating parameters affect performance. They can then use this information to optimize operations, improve performance and increase productivity. For example, a digital twin of the oil extraction process can help operators identify bottlenecks and optimize extraction rates.
- Asset Optimization: Digital twin enables operators to make the most of critical oil and gas assets. A digital twin of an oil field can help operators better understand field behavior and plan mining strategies more effectively. This method leads to higher mining rates and increased profits for the business.
- Safety and emergency preparedness: Safety is an important issue in the oil and gas industry, and digital twin technology can improve safety in many ways. The digital twin will simulate a range of scenarios to help operators optimize operating procedures and minimize potential risks. For example, a digital twin of an oil pipeline system can help predict risks of leaks or ruptures, allowing operators to repair pipelines before dangerous incidents occur.
- Sustainability: The oil and gas industry is facing increasing pressure to reduce its environmental impact. Digital twins are an invaluable tool in this effort. By simulating operations and their impact on the environment, businesses can develop strategies to reduce emissions, manage waste, and comply with environmental regulations. It can also simulate the impact of new regulations and/or technologies, helping the industry continue to adapt as technology advances and develops.
- Optimize drilling operations: Drilling operations are complex and expensive. Digital twin technology can help optimize these operations by simulating different drilling scenarios and providing information on the best strategies. For example, a digital twin of a drilling operation can determine the optimal drilling speed and drilling direction, improving the overall accuracy of the drilling process.
- Field management: By creating a digital twin of an oil field, operators can visualize field behavior, optimize drilling strategies and maximize production. This method not only optimizes the mining rate but also prolongs the life of the mine.
- Supply chain optimization: Oil and gas supply chains are complex. Maintenance teams can use digital twins to simulate the entire supply chain, providing insight into operations and logistics and identifying potential obstacles.
- Design and test new systems: Designing and testing new equipment and systems can be an expensive and labor-intensive process. With digital twins, engineers can design, test and perfect new systems in a virtual environment before they spend time and money building them. Using a digital twin in this way can significantly shorten the development cycle and improve the performance of the final product.
- Training and skills development: Digital twins can serve as a practical training tool for industry employees. For example, a digital replica of a complex oil refinery—when integrated with VR technology—can provide a realistic environment for employees to train and perfect their skills, improving safety practices. integrity and overall quality of products and processes.
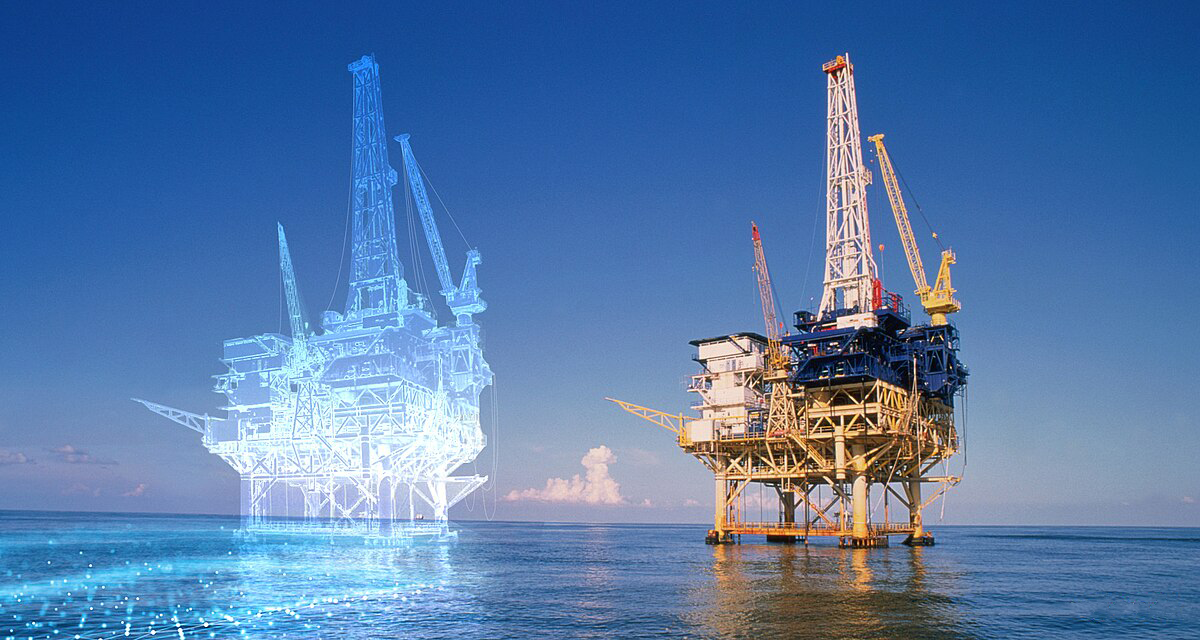
The Future of Digital Twin Applications in the Oil and Gas Industry
As the industry continues to embrace digital transformation, the role of the digital twin is expected to grow strongly. The potential of this technology will be increasingly enhanced in parallel with the increasing adoption of technologies such as artificial intelligence (AI), machine learning and Internet of Things (IoT). Furthermore, with the emergence of cloud computing—which reduces the need for large investments in IT infrastructure—deploying a digital twin is becoming more feasible for a wide range of companies.
Looking to the future, we know that digital twins will play a vital role in process automation. Combining this technology with robotics and automation systems can lead to fully automated drilling operations. Similarly, digital twins enable the development of smart grids in gas distribution systems, making supply chain optimization more efficient and reliable.
As the industry faces an increasingly urgent call for sustainable environmental practices, the digital twin can also be the foundation for the transition to cleaner and more renewable energy sources. Digital twins of wind masts, solar panels or entire renewable energy grids have the potential to improve overall efficiency, making these energy sources more competitive with fossil fuels.
And in search, digital twins could revolutionize the way companies search for new oil and gas fields. With a digital replica of the Earth’s subsurface, oil and gas companies can accurately predict the location of new natural gas and oil deposits, reducing the costs and risks associated with finding them. .
However, to fully realize these capabilities, the industry must overcome several hurdles. Companies will need to invest in developing digital skills for their workforce and address complex issues related to data ownership, privacy and security. They also need to foster a culture of innovation and flexibility, as the digital revolution will bring significant changes to traditional ways of working.
Despite the challenges, the potential benefits of digital twins are too important to ignore. As the oil and gas industry navigates the path of digitalization and sustainability, digital twins promise to be a powerful tool in the industry’s arsenal. By providing a window into the future, they can help the industry anticipate, prepare for and shape the changes that are coming.
IBM Maximo Application Suite–Digital Twin Technology Management
The era of digital twins in the oil and gas industry is just beginning. By providing a real-time link between the physical and digital worlds, they enable operators to understand, predict and execute systems like never before.
However, digital twin management can be a complex process, requiring advanced software solutions like the IBM Maximo Application Suite. IBM Maximo is an integrated platform that helps service providers optimize asset performance and optimize daily operations. Using an integrated platform based on artificial intelligence and the cloud, Maximo provides CMMS, EAM and APM capabilities that create advanced data analytics and enable smarter data-driven decisions across facilities. oil and gas exploitation and production.
As exciting digital technologies continue to develop, digital twins will redefine the future of the industry. With IBM Maximo, your business can leverage digital twin technology to build a more efficient, sustainable and prosperous future.
IBM Authorized Dealer Consulting on Enterprise Asset Management Solutions in Vietnam
Vina Aspire is a consulting company, providing IT solutions and services, network security, information security & safety in Vietnam. Vina Aspire’s team includes skilled, qualified, experienced and reputable experts and collaborators, along with major domestic and foreign investors and partners to join hands in building.
Businesses and organizations wishing to contact Vina Aspire Company with the following information:
Email: info@vina-aspire.com | Website: www.vina-aspire.com
Tel: +84 944 004 666 | Fax: +84 28 3535 0668
Vina Aspire – Vững bảo mật, trọn niềm tin